-
-
-
-
-
Service
-
Common problems and solutions of calcium carbonate in plastics
The important role of calcium carbonate in plastics. China has become a major producer and consumer of plastic products. In 2006, the output of plastic products exceeded 40 million tons, ranking second in the world, and has maintained a double-digit annual growth rate for more than 20 years. It is foreseeable that with the increase in domestic consumption demand and the increase in exports to the international market as a global manufacturing base, the annual output of plastic products in China will continue to grow rapidly for a considerable period of time in the future. In the plastic processing process, in addition to synthetic resins as basic raw materials, the scientific, correct, and reasonable use of various additives and auxiliaries is undeniable, including
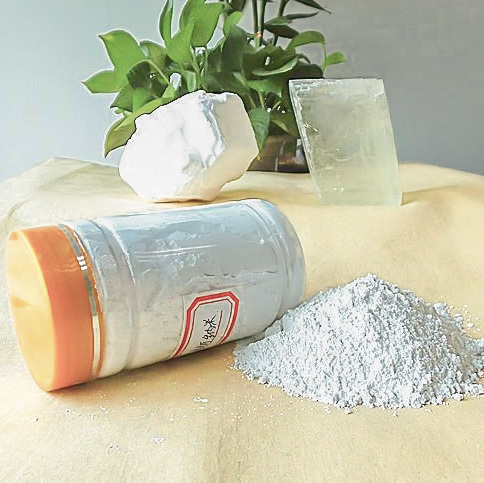
Related products
Online consultation
We will consistently provide you with high-quality calcium carbonate products, honest service style and reasonable product prices. If you have any questions, please feel free to leave a message!
*Note: Please be sure to fill in the information accurately and keep the communication open. We will contact you as soon as possible.
CONTACT/Contact
Telephone:0571-58318388 / 58300688
Email:1192621536@qq.com
Address: Li Jia Town Industrial Functional Zone, Jiande City, Zhejiang Province
%E7%AC%AC%E4%B8%80%EF%BC%8C%E6%9C%80%EF%BC%8C%E4%BC%98%E7%A7%80%EF%BC%8C%E5%A2%9E%E5%BC%BA%EF%BC%8C%E4%B8%80%E6%B5%81%EF%BC%8C%E5%8D%93%E8%B6%8A%EF%BC%8C%E9%A2%86%E5%85%88%EF%BC%8C%E5%85%88%E8%BF%9B%EF%BC%8C%E5%BC%95%E9%A2%86
Sorry,当前栏目暂无内容!
您可以查看其他栏目或返回 首页
Sorry,The current column has no content!
You can view other columns or return Home